Building Energy Resource Hub Case Study: Plant Chicago
Project Overview
Location: Chicago
Official Building Name: The Firehouse
Year Built: 1907-1908
Year When Retrofit Began: 2025
Total project cost:
$1.3 million* New roof: $56,000
Solar array: $25,000
Air source heat pump: $100,000
Financial incentives leveraged:
Neighborhood Opportunity Fund: $500,000
Climate Infrastructure Fund: $250,000
State of Illinois appropriations: $300,000
Landmark Illinois loan: $300,000
* Current cost estimates; likely to change.
Project Team:
Architect of Record: Maria Bergh, We Build Agency
Design Architect: Maria Bergh
Developer: Plant Chicago
Engineering Lead: dbHMS
Other Engineers: Rocky Structures
General Contractors: Toro Construction, Naturally Urban Environmental
Project team 80% minority-owned or women-owned businesses
Background
In the Fall of 2019, Plant Chicago—a nonprofit that works to cultivate local circular economies—moved from its longtime space at a collaborative small business facility to its new home at an old Chicago Firehouse at 4459 S. Marshfield Ave. in Back of the Yards.
Originally constructed between 1907 and 1908, the building was home to the Chicago Fire Department’s Truck Company 33 until 1978, when the company was one of the last to motorize its operations and move away from horse-drawn carriages. The Firehouse then went through a series of owners, all of whom made their own un-permitted renovations.
When Plant Chicago moved in, the Firehouse had been unoccupied for about a decade. “There was half standing water in the basement, the heaters weren’t working, it was a pretty rough space. We had to work on making it habitable for us first,” says Eric Weber, Plant Chicago’s director of operations.
When the chance to purchase the building came up in 2022, the team jumped on the opportunity and began making plans for a more substantial retrofit. Plant Chicago runs an indoor urban farm and a store for local merchants, as well as education programs centered around the circular economy, so it had specific needs for the space.
And while the organization’s mission focuses on sustainability, the Plant Chicago team did not originally plan for a decarbonization retrofit until they were made aware of the availability of grant funds tied to specific building sustainability improvements.
This case study explores the green upgrades that Plant Chicago has already completed as well as the next phase of the decarb retrofit project, which is ongoing at the time of publication. It also dives into the challenges around code compliance and grant funding requirements that the team has experienced, and outlines lessons for other building professionals who are working on their building decarb journeys.
Phase 1: Roof Replacement and Solar Installation
The first major investment that the Plant Chicago team embarked on was the replacement of the Firehouse’s main roof. They were originally approached by Renewable Energy Evolution, a company that works with nonprofit organizations to leverage financing opportunities through programs such as Illinois Solar For All to install onsite renewable generation, about setting up a solar array on the roof. Since the team had no idea how old the roof was, and was hesitant to install new solar panels atop a questionable foundation, the roof replacement became priority number one.
And while the team expected there to be at least two to three layers of roofing material stacked on top of one another from short-cut replacements over the years, they were shocked to find they had 11 layers of roofing—a total of 20 tons of material—to tear off before the new roof could be installed.
“We noticed so much change just from having the building be able to breathe again,” Weber says.
The roof replacement ended up costing $56,000, and the new roof, along with the solar array, were finished by the end of 2021. After passing inspections, the solar array was turned on and operational in early 2022.
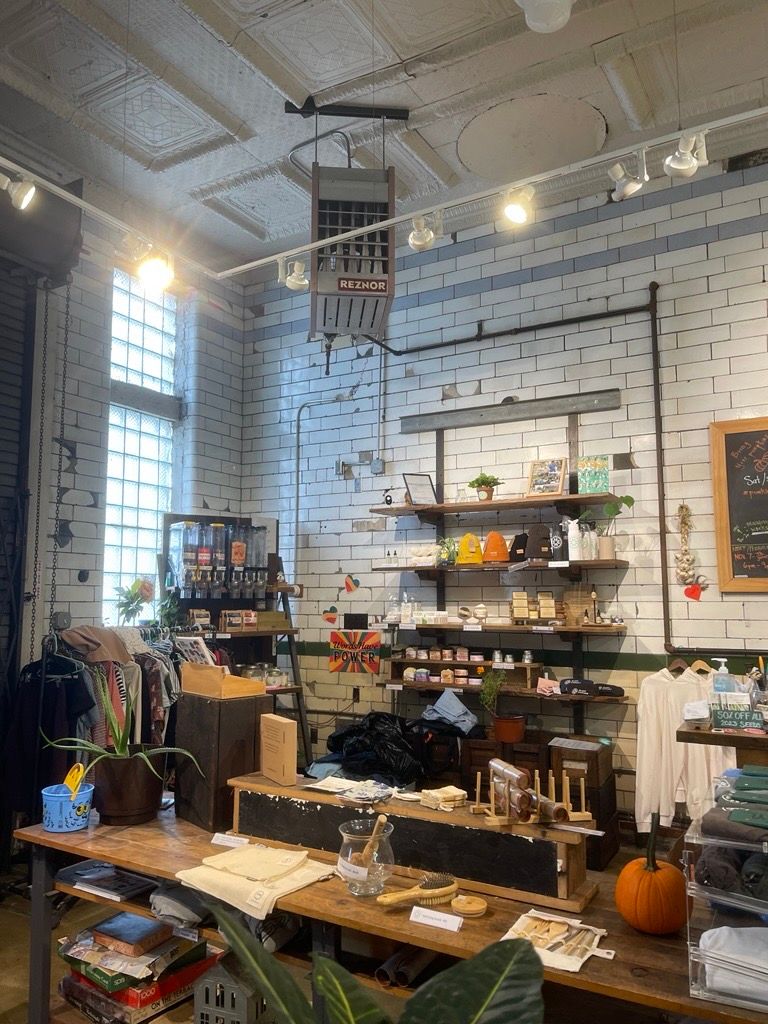
Phase 2: Decarbonization Renovations
The second phase of the project, which began in early 2025, includes a far larger list of improvements that focuses on decarbonization, efficiency, accessibility, and functionality.
The goal is to decarbonize roughly 90% of the building (the entire first floor and basement) by replacing the aging gas-powered heater with a new air source heat pump system, and the gas hot water tank with a hot water heat pump. At the same time, the project aims to increase the building’s overall efficiency and performance by improving the envelope, incorporating daylighting through new windows, and upgrading to LED lighting—among other measures.
The team decided against fully insulating the first floor of the main Firehouse building, since they would have to remove and replace drywall in certain areas and in others, insulation would cover the original exposed brick—which gives the space much of its unique aesthetic appeal. Insulation will be added to the roof and walls of the adjacent single-story addition, which houses the indoor Victory Garden.
They will also focus on tuck pointing the exterior of the building, where some of the mortar has deteriorated over the years, allowing a significant draft to get indoors. On top of that they are upgrading the exterior doors to increase insulation.
A previous owner had bricked over many of the original first-floor windows, so the project team will be installing new windows along the south facade that will provide additional ventilation as well as plenty of natural daylight, which can help reduce energy used for heating and cooling.
As part of the project, the indoor Victory Garden will be moved from its original home in the main first-floor space of the Firehouse to the adjacent single-story addition, which was originally built as a garage. This existing garage space therefore needs to be retrofitting for indoor farming, including all new plumbing, electrical, floor drains, and HVAC.
Much of the remainder of the work for this second phase revolves around accessibility. Since Plant Chicago was leveraging city funds for the project, a certain percentage of those funds needed to go toward accessibility upgrades—which also aligns with the organization’s mission. The renovation will ensure that doors are ADA (Americans with Disabilities Act) accessible and upgrade two bathrooms on the first floor to be ADA accessible.
Creative Financing Challenges
The main driver for Plant Chicago to be able to launch this project was the receipt of a Neighborhood Opportunity Fund (NOF) grant from the city of Chicago. The NOF provides grants to small business, nonprofit, and cultural projects located along South, Southwest, and West Side commercial corridors.
The NOF grant requires the recipients to provide matching funds equal to the award, and so Plant Chicago was able to qualify for $500,000 in grant funding matched by the $500,000 purchase of the building. This helped fund much of the design and prep work, as well as a good portion of the other upgrades.
A challenge that arose around the NOF was that the program is broken down into two segments: small projects and large projects, with large projects having additional reporting and compliance requirements. Even though the amount of money that Plant Chicago requested was within the scope of a smaller project, they had to apply for the large program because the site was not located within the geographic boundaries set out for the small program. This meant had to jump through additional hoops—which are explored further in the next section.
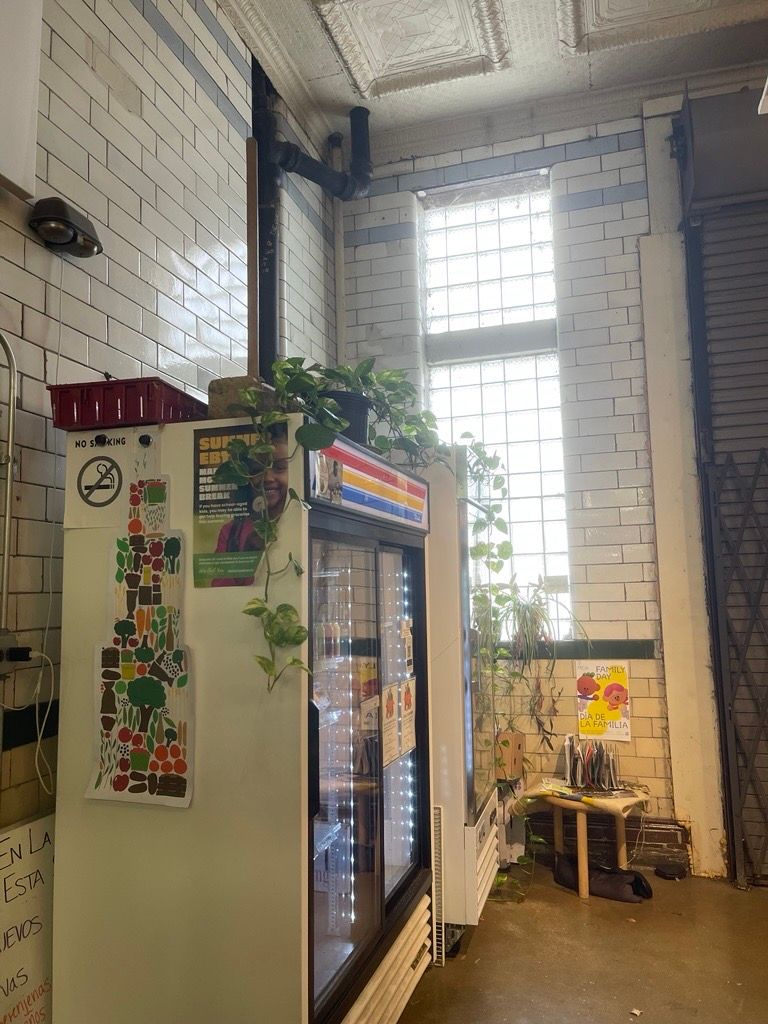
Through the federal Inflation Reduction Act, the city of Chicago received funds to promote building decarbonization and sustainability projects as part of the city’s overall climate goals. Plant Chicago was awarded $250,000, which went toward funding the upgrade of the heat pump HVAC system as well as other specific sustainability measures on the project.
Finally, the Plant Chicago team worked with their state representative, Theresa Mah, to apply for and receive a $250,000 grant from the state of Illinois for additional sustainability work. This raised their grant funding total to $1 million. However, these funds are only released when the state sells bonds, and as of the printing of this case study those funds have not been released yet.
Plant Chicago secured a bridge loan from Landmark Illinois in order to access the funding before the state money is released, and will use the state grant to repay the loan. This is another demonstration of the challenges that nonprofits and other organizations that work in disadvantaged communities must deal with in order to complete building decarbonization and sustainability projects.
Navigating Code Compliance
One of the other main challenges on the retrofit project is that the previous owners did not permit their improvement work thoroughly over the years, so the team not only needs to correct past mistakes but also ensure the next phase of the project is compliant.
Plant Chicago’s experience working with Chicago’s Department of Buildings around code compliance and permitting has been reflective of the struggles that other developers have had in terms of getting their projects across the finish line. As part of the NOF grant scope of benefits, Plant Chicago’s team had the opportunity to consult with city code officials to review their plans and get pre-approved to ensure early compliance.
The team thought this would help them cover all of their bases early on in the project planning stage. However, there have been a number of inconsistencies between what the project team was told during the initial review and the site review that occurred as they were beginning to start work, which has caused delays in the project and driven up its cost.
For example, Plant Chicago’s property spans three separate lots—the Firehouse building and the adjoining garage/indoor farm space are two lots zoned for commercial, while the third lot that features a chicken coop and garden is zoned for residential. This discrepancy was not flagged during the initial review process but was called out eight months later.
“Being at someone’s whim, if you get a code reviewer on a bad day, could totally change the outcome,” Weber says.
Another challenge has centered around the delays in the process of correcting even minor issues on the files that the design team submits to the city. As it stands, when the code reviewers send a file back to the design team for even the smallest of technical corrections, that file is then sent to the back of the line of paperwork that that reviewer is managing, which can then take months to be reviewed again.
“I don’t know that all the reviewers understand that if they have a very minor issue, and they send it back, that can delay the project by like two to six months, and I don’t think they realize that a two-to-six-month delay can raise costs by anywhere from 20-30 percent,” says Maria Bergh, lead architect on the project. Having a more direct line of communications between project teams and city building officials for correcting small technical issues could help speed up the process and ensure projects remain within budget.
Finally, the goal for the indoor farm is to have USDA food production space so that growers can sell their produce directly to the public, which adds another layer of complexity. Fortunately, the project team engineers have experience designing growing spaces and were able to navigate through these issues.
Lessons Learned
The journey that Plant Chicago has been on to secure funding, meet requirements attached to that funding, and comply with building codes and city permitting offers many lessons for other AEC professionals, nonprofits, and small businesses as they embark on building decarb projects.
The first is to expect delays and to bake the additional time and cost into your calculations. “You want it to go fast, you hope it could, but it’s likely not going to,” Weber says. “When all is said and done, we’ve had three to four years of intensive and purposeful work on it and that’s just for a relatively small project when it comes down to it. That’s my big thing—don’t get frustrated by how long it will take.
For AEC professionals working with smaller clients, Bergh says to “be brave, build relationships first, and explain in detail how much unknown risk is a part of the building and permitting process. Talk to the building department early but focus on keeping the project moving as fast as possible.”
This will ensure that clients are not surprised by unforeseen delays or work that is added to the scope to comply with local regulations. Based on this experience, Bergh recommends hiring a permit expediter if possible and being conservative with how the code is interpreted and applied. It’s also best practice to list code references “copiously” on the drawings.
In order to make projects work on a tight budget, AEC professionals can also suggest that their clients phase a project instead of taking it on all at once. And to be as prepared as possible for any outcome, ask the client to prepare to raise 25-50% more than their initial budget, particularly as rapid inflation can quickly raise the cost of an ongoing project.
The city of Chicago and the Department of Buildings could also take valuable lessons away from Plant Chicago’s experience. Much of the project team’s frustrations centered not around complying with the code itself, but with the inconsistencies of what they were told from one building employee to the next.
Chicago has admirably set out extensive climate goals attached to generous funding opportunities, and has a vested economic and financial interest in seeing projects like this succeed across the city—particularly in neighborhoods like Back of the Yards.
It is therefore counterproductive for the building department to cause confusion around code compliance and create unnecessary delays through antiquated filing review practices. A review of the city’s permitting and review processes, with an eye toward how other large city building departments operate, could help speed up projects, save teams money, and create more economic development across every corner of the city.
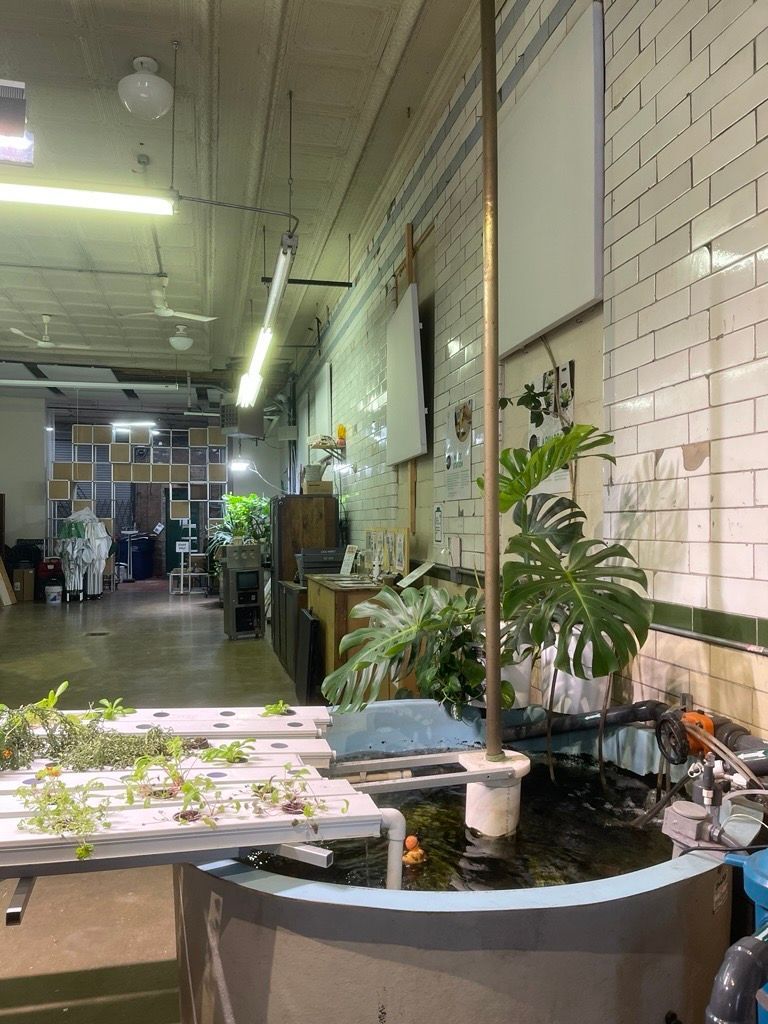