Decarbonization Planning Guide
Develop Your Decarbonization Plan
Electrifying Building Systems
How to make your building independent of fossil fuels.
Electrification is the process of replacing the equipment within a building that uses combustion from fossil fuels to alternatives that solely run on electricity instead. When the equipment burns fossil fuels directly, such as a gas boiler, we call this onsite combustion—and it’s a primary driver of most buildings’ GHG emissions.
It’s possible the electricity that powers your building comes from a plant that burns fossil fuels, too. This isn’t onsite combustion, but it still contributes to GHG emissions.
However, as more and more electricity on the grid comes from renewable sources, the emissions from using electricity will eventually reach near zero. With some technologies, such as heat pumps, emissions are already lower compared to equipment that uses onsite combustion. Addressing the equipment in your building that uses onsite combustion is critical to your decarbonization plan.
The major building systems which typically use onsite combustion are space heating, domestic hot water, cooking, and certain processes unique to the building.
Each of these areas has different considerations when it comes to potential alternative systems, enabling needs, operating parameters, and costs.
Why You Should Electrifying Heating
Heating accounts for 35% or more of a typical building’s GHG emissions. Without converting boilers or gas heaters to a low-emissions energy source, you’re missing out on a big chunk of potential in your decarbonization plan.
The figure compares the emissions of a building with electrified heating to a building that only implements energy efficiency measures alone, without electrifying its heating.
As we move forward in time, emissions from heating and other onsite combustion uses (such as cooking and domestic hot water) eventually reach a limit on how much they can reduce emissions—since, after all, they continue to burn fossil fuels. However, electrifying heating helps the building reduce its emissions much more dramatically, since the building will get more and more energy from renewables on the grid and has less onsite combustion.
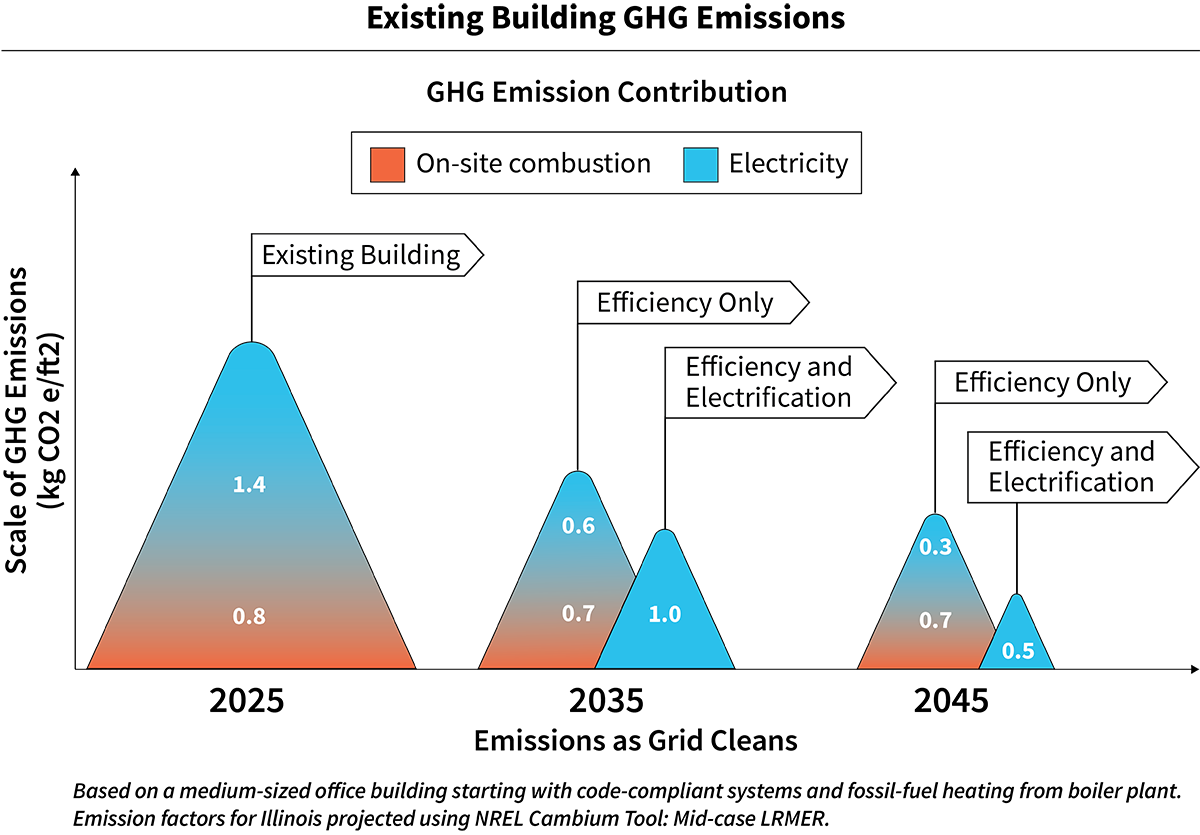
HVAC
Electrifying a building’s HVAC system usually means replacing fossil fuel equipment such as boilers, AHUs, and furnaces with heat pumps.
However, electrification is not always as simple as changing equipment. For example, a building might need new electrical infrastructure to accommodate the additional electrical load. A building might need load reduction measures so that heat pumps can be sized smaller and have less impact on your utility costs from peak loads. Ductwork or hot water (or steam) pipes might have to be replaced to handle changes in water or air temperatures.
More information on some of these measures to ready your building is available in the load reduction and enabling sections. Successful HVAC electrification requires viewing the entire building as a system and not just the sum of its parts.
While planning for electrification, consider additional value adds that may coincide with a new HVAC system and holistic decarbonization plan. For instance, when equipment gets replaced, reconfigure the ventilation system to improve indoor air quality while incorporating heat recovery.
Several potential solutions exist to electrify your building’s HVAC system that are applicable to Illinois’ climate. These include heat pump RTUs, geothermal solutions, split or packaged air source heat pumps, and variable refrigerant flow (VRF)_ systems to provide heating and cooling.
Ventilation can come from air handling units, dedicated outdoor air systems, or make-up air units, depending on the existing building configuration and goals of the project. If you’re looking beyond a simple replacement, you’ll likely need a detailed assessment and design from an engineer.
Partial Electrification
Of course, fully electrifying a building’s HVAC system is often impractical or simply too expensive. In these cases, partial electrification is often a good option.
Partial electrification can achieve many of the benefits of full electrification while saving on initial costs and requiring less extensive work on the building. For instance, heat pumps could be designed to meet most of the building’s heating needs while a gas furnace serves as a backup for only the coldest days with the highest heating loads.
How partial electrification can be implemented depends on the type of HVAC system you have. For systems with packaged equipment such as Rooftop Units (RTUs), a typical option is a dual-fuel RTU, which is a heat pump with a backup furnace. In hot-water heating systems, this dual-fuel setup is often accomplished by leaving the existing boilers in place, reserved for firing up only in the event the heat pumps can’t keep up with the heating load. A buffer tank or thermal storage may be needed to accommodate the air-to-water heat pump system and expand when it’s able to run at optimal conditions.
Because heat pumps will run most of the time, thereby reducing emissions compared to onsite combustion, partial electrification is a good solution for buildings with modest capital budgets or with features that make it challenging to fully electrify. These systems may also be designed to accommodate full electrification in the future.
Key HVAC Electrification Questions
- Should I install a centralized or distributed electric HVAC system?
- Am I adding air-conditioning or ventilation to the building?
- Do I want to also achieve non-energy benefits like cleaner indoor air or greater thermal comfort?
- Should I add or change ventilation to my building?
- If my building needs heating and cooling at the same time, should I add a heat recovery chiller?
Domestic Hot Water
There are several different options for electrifying Domestic Hot Water (DHW) systems. The most appropriate one for your building depends on several factors including the building’s size and occupancy patterns, the configuration of existing systems, and installation and utility costs.
The largest difference between hot water systems is whether they are centralized systems or distributed systems. Centralized systems take a single source of hot water and distribute it throughout the building. Distributed systems use multiple smaller water heaters throughout the building, usually located close to where they’ll be used. These smaller heaters are usually electric resistance heaters without water storage.
Distributed systems have some advantages compared to centralized systems:
- You don’t have to install distribution piping through the whole building—just a few feet of piping at each point of use.
- Maintenance and repairs usually affect one heater, rather than the entire system.
- A water heater can be connected to a tenant’s electrical panel, passing the cost of hot water directly to the tenant.
However, centralized systems have their own advantages:
- They usually have more heating capacity than distributed systems, making them better suited for high-use buildings.
- Distributed systems sometimes fail to keep up with long, continuous temperature draws, meaning that water temperature starts to fall during times of extremely high demand.
- Centralized systems with storage can take advantage of an electric utility’s demand or time-of-use pricing (or requested demand response) by turning off the water heaters and distributing hot water from storage tanks, therefore saving money on utility rates.
The system that works best for your building depends on its needs. Distributed systems are often used in office buildings and ground-floor retail. Centralized systems tend to be better for high-occupancy or high-use buildings such as multifamily, medical, and food service, as well as buildings with special water uses such as laundromats.
Heat Pump Solutions
Heat pump water heaters (HPWHs) come in several different varieties, from residential-style models with integrated storage tanks to large air-to-water heat pumps designed to be part of a larger system. Some heat pumps designed for space heating can even heat water at the same time.
Partial Electrification
When applied to DHW system, dual-fuel heat pumps typically only require fossil-fuel backup for a few hours of the year when the building’s demand for hot water is at its highest. As with HVAC, these systems can reap most of the benefits of fully electric systems while requiring less investment to convert the existing system.
Key DHW Electrification Questions
- What type of building am I electrifying? (Office? Apartment? Condo? Hospital?)
- How much of the day or week is the building occupied?
- Is there a single occupant or many tenants?
- Is a recirculating or centralized DHW system already in the building?
- Does the building have a commercial kitchen or other high hot water user?
- Is there space in the mechanical room for a central water heater, or is there space to expand the mechanical room?
Cooking and Miscellaneous
Cooking is another common use of onsite combustion within a building. In buildings with commercial kitchens, the impact from cooking alone can be a significant driver of the building’s overall emissions.
Many kitchen appliances have all-electric versions that still meet the standards of a professional kitchen, such as induction ranges, combination and conveyor ovens, and convection ovens.
Using electric equipment also brings non-energy benefits to the occupants in the kitchen:
- The air is cleaner since there is less (or no) combustion in the kitchen.
- Air temperatures can be lower due to more efficient equipment, improving comfort and reducing the building’s cooling needs.
- Replacing gas cooktops with induction reduces the risk of fire and burns.
- Induction does not warp or damage pots and pans, reducing replacement costs for cookware.
Another major use of combustion equipment are commercial laundry systems. Heat pump dryers are becoming widely available and can reliably dry linens at commercial throughput levels. Heat pump dryers operate at lower temperatures and consequently don’t need exhaust venting; for that reason, they are also sometimes called “ventless dryers.” Because of the lower drying temperatures, they also pose less of a fire risk.
Refrigerant Considerations
As you phase out sources of onsite combustion, it’s likely that your heat pump equipment will use refrigerants work properly. There are various types of refrigerants, each with its own global warming potential (GWP)—adding another element to consider regarding your building’s environmental impact.
Selecting low impact refrigerants and managing leakage is very important, as some hydrofluorocarbon (HFC) refrigerants can have upwards of 2,000 times the GWP of carbon dioxide. Changes to the types of refrigerants include the addition refrigerants classified A2L (low flammability) will impact equipment selection and monitoring practices within commercial building.
Top considerations include:
- Work with a design team to select equipment that reduces the amount of refrigerant used based on type and size.
- Utilize low to no GWP refrigerants.
- Work with HVAC contractors to ensure best practices in installation and maintenance.
- Set up a refrigerant tracking system to record how much refrigerant is filled and when. This can help identify when systems are leaking refrigerant.
You can find more information on the upcoming EPA phasedown of HFC refrigerants here.
Future proofing considerations
Even if you plan to fully electrify, partial electrification of systems can provide a starting point, allowing you to make headway on decarbonization while raising more capital for full electrification.
In addition to helping a building meet peak HVAC loads, thermal and battery storage can continue to provide HVAC and other building services during a power outage, making the building more resilient.
Consider investing in low-flow fixtures to reduce DHW demand, reducing the required capacity of a heat pump DHW system.
Additional considerations
There’s more to a piece of equipment than its efficiency and energy source. There’s also its
embodied carbon emissions, which are the GHG emissions associated with manufacturing and delivering the equipment throughout its supply chain.
For the purposes of your decarbonization plan, you can consider existing equipment in the building as having no embodied emissions, since it’s already installed. If existing equipment—such as ducts, pipes, and radiators—can be reused and refurbished, it will help keep embodied emissions low—plus you’ll save some money on the replacement costs.
Links to Resources
HVAC
- Building Energy Resource Hub Technology Primers provide additional information on an array of HVAC solutions.
- NREL/ASHRAE Thermal Systems Guide
Domestic Hot Water
Cooking
- New Buildings Institute All-Electric Kitchens Webinar and Presentation
- The Building Decarbonization Practice Guide (The Worthen Foundation) – This free, downloadable guide to decarbonizing buildings includes a volume with detailed discussions of electric kitchen improvements and case studies.
- The ENERGY STAR Commercial Kitchen Equipment Resource Hub includes a product and rebate finder, a list of partner dealers and distributors, and a savings calculator for upgrading to ENERGY STAR equipment.