Building Energy Resource Hub Case Study: 401 North Michigan
Project Overview
Location: Chicago
Owner: Walton Street Capital
Property Manager: Zeller
Year Built: 1965
Building Type: Commercial
Square Footage: 746,131 sq. ft.
Certification: LEED Platinum
Performance Data: All 2022 LEED Platinum Recertification-related Projects
Annual energy use reduction: 77,563 kWh
Annual CO2 emissions reductions: 55 metric tons
Energy reductions compared to 2018/2019 baseline:
- 13% of kWh
- 36% gas usage
Total annual financial savings (gas and electricity): More than $100,000
37% more efficient indoor plumbing fixtures than national standards.
89% of building occupants bike, walk, or take public transit to work.
Background
Situated at the confluence of the Chicago River and the iconic Magnificent Mile, 401 North Michigan is blessed with one of the most prominent, and historically important, sites in the city. Chicago’s first permanent resident, Jean Baptiste Pointe du Sable, built his personal residence and fur trading post there in the late 1770s. Today, it serves as the gateway between the city’s Loop business district and the dining, shopping, and entertainment mecca of River North.
Yet in today’s challenging commercial real estate market, even properties with the most distinguished locations are being targeted by owners and management for upgrades to stay competitive with tenants and potential investors. Many owners and managers of large office buildings are turning to sustainability upgrades, retrofits, and green certifications that improve overall building performance and reduce energy costs and emissions.
That was the strategy employed by Zeller, the firm managing 401 North Michigan. Designed by the renowned architecture firm Skidmore, Owings & Merrill and completed in 1965 as the Equitable Building, the structure has gone through extensive renovations in 1990, 2012, and again in 2016. The 2016 renovation included certification for LEED Platinum, the highest rating level for LEED green building certification. In 2022, 401 North Michigan achieved Platinum recertification as Zeller continued pursuing energy efficiency and sustainability investments.
Energy Efficiency Investments and Upgrades
Rather than embark on a costly and disruptive full-building energy efficiency retrofit, Zeller has approached sustainability upgrades as part of a continuous and ongoing process along with traditional building maintenance.
Each year, whenever an energy efficiency opportunity or sustainability initiative was presented to us, and if it was economically achievable, it became our map to qualify and earn credits to cross the finish line—whether for [LEED] Gold or Platinum,” says Lori Olson, Vice President and General Manager at Zeller.
Many of those opportunities come in the form of free local utility programs, such as ComEd’s facility assessments, rebate programs, and retrocommissioning services, which help building owners and operators identify ways to improve energy efficiency and building performance.
Performance Improvement Highlights
- Retrocommissioning
- Building controls
- Steam trap audit
- Scheduling optimization
- Lighting level adjustments
- Wireless pneumatic thermostats
- Space optimization
- Leak detection
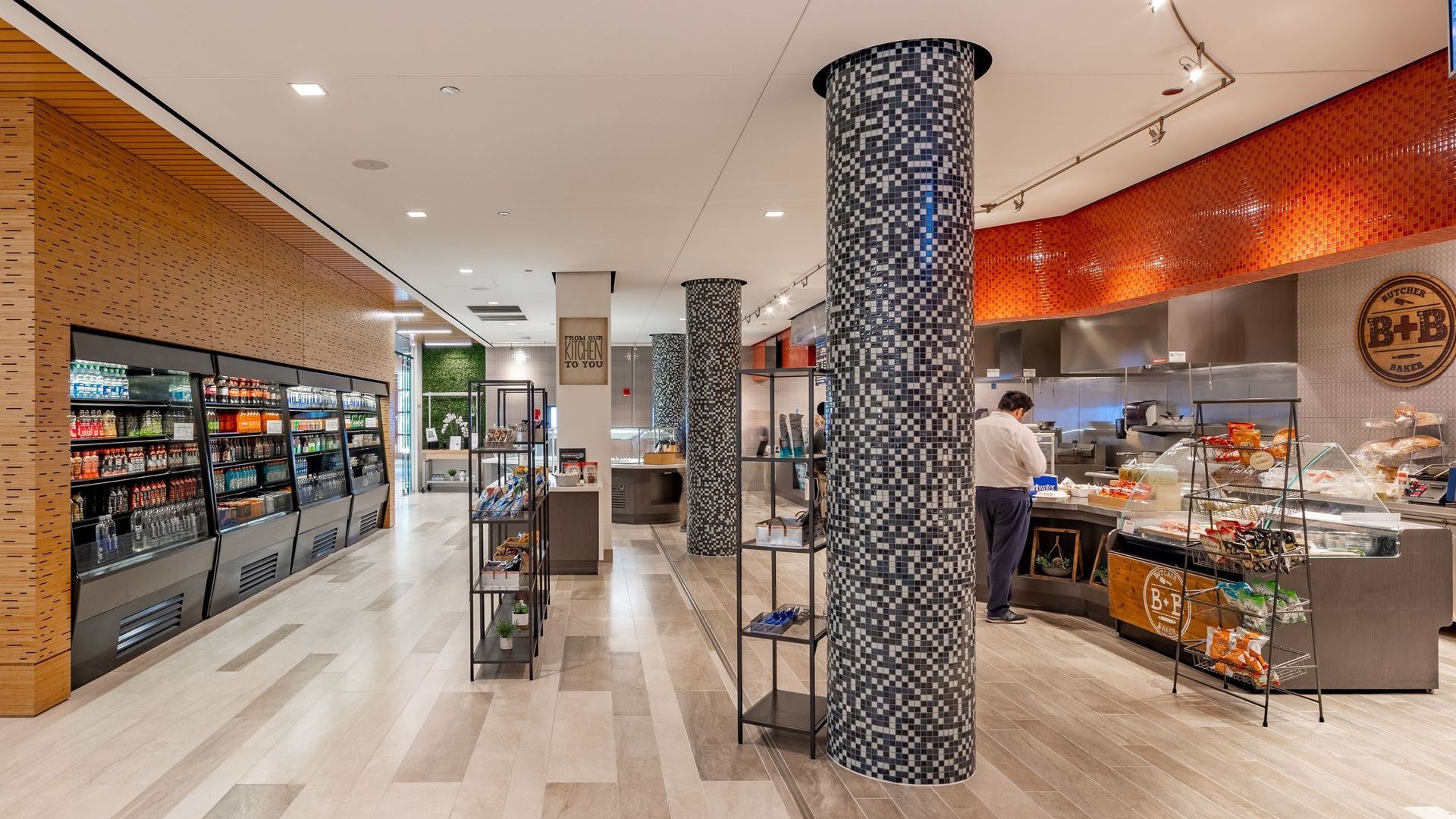
One system that was a prime candidate for an energy efficiency upgrade was the building’s thermostat systems. Previously, building operators could not communicate directly with the building’s more than 650 thermostats. The engineering staff at 401 North Michigan worked closely with a controls contractor to replace all existing thermostats with new wireless pneumatic thermostats (WPT) that they can directly monitor and control.
Prior to the upgrade, there were days when building engineers had to stick to a general whole-building schedule of heating in the morning and cooling in the afternoon, which is highly inefficient and ignores the needs of individual tenants. With the new WPT system, building operators can use the real-time data it provides to adjust temperatures in individual spaces—for example, lowering the heating/cooling in offices on days when the tenants work from home. This has not only saved energy and money but also improved tenant comfort.
Another simple yet impactful way to lower energy costs and emissions was to update the light fixtures in the building’s stairwells, mechanical spaces, and underground garage, given the lower levels of traffic in these areas. Zeller replaced all the fixtures with LED lighting—which uses substantially less energy than incandescent bulbs and lasts up to 25 times longer—and incorporated motion sensors into these systems so that full lighting is only used when someone enters the space. When these spaces are empty, lighting goes down to 20% of full capacity.
Project Challenges
One of the main challenges with upgrading a nearly 60-year-old commercial building is that the age and complexity of many original systems, such as high-pressure steam boilers and turbines, means they cannot be integrated with new technology to drive efficiency. And given the enormous costs involved, building owners and managers are hesitant to invest in new systems before the existing systems reach the end of their life cycle.
“If the challenge with the older equipment can’t be overcome short of replacement, then it’s just staying on top of control strategies and exploring how we use the system in the most efficient way,” Anderson says. Keeping staff trained on the cutting edge of best practices in operational sustainability can help bridge the gap until ageing systems are ready to be replaced.
Another challenge for achieving LEED certification for existing buildings is the requirement to gather feedback from a certain percentage of tenants via a survey. Tenants are busy with their own operations and may not prioritize responding to a detailed survey shared by building management. Surveys can include questions about energy use, occupancy times, and the number of employees who take public transit or use the bike room, among others.
Anderson has used building town hall meetings as a forum to highlight the importance of completing the surveys for tenants. Building staff has handed out surveys during tenant engagement activities—such as pumpkin carving contests—and leveraged these social opportunities to explain the need for participation and answer any questions tenants may have.
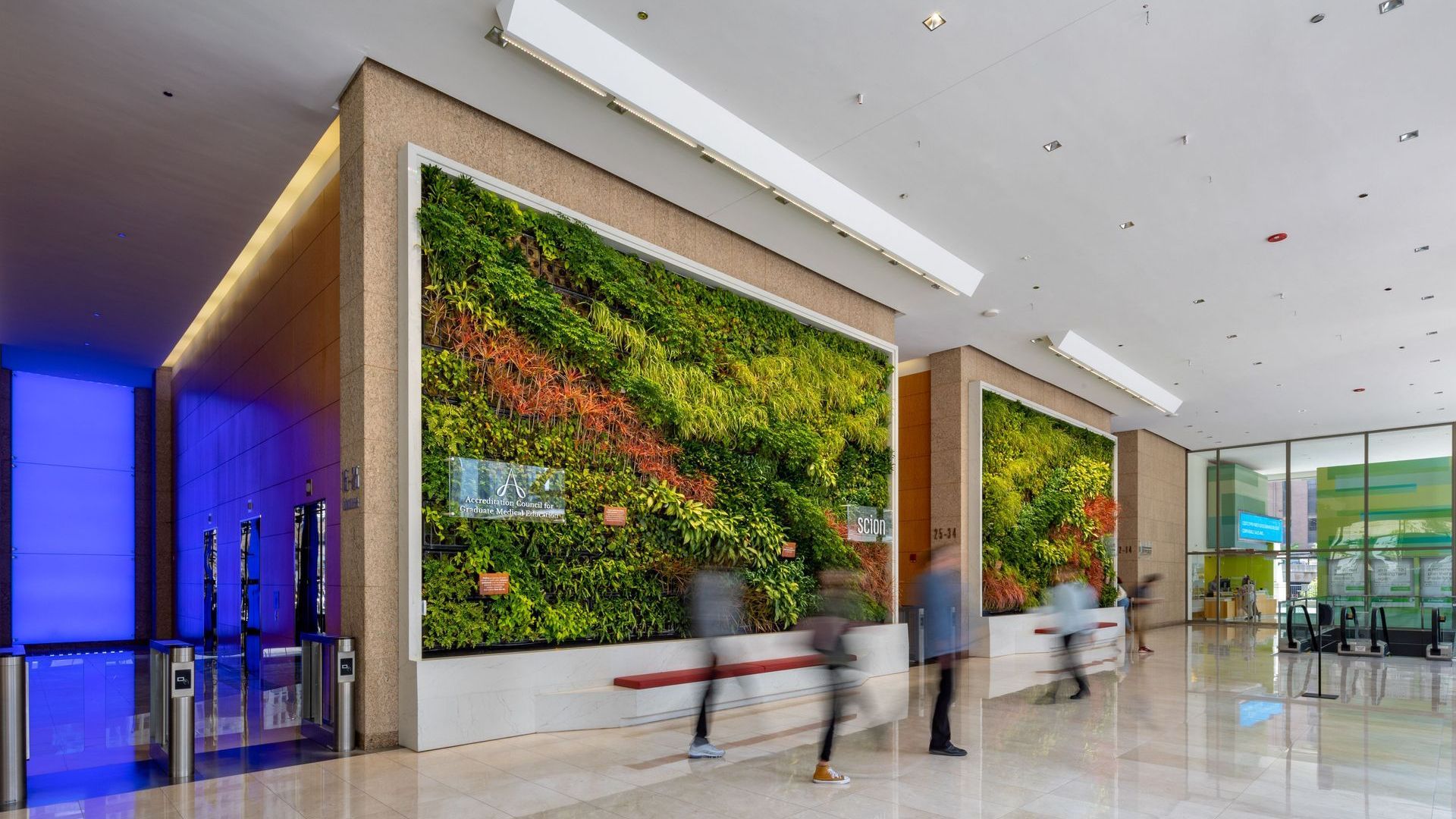
Operations Staff Engagement and Training
One of the keys to the success of the sustainability investments at 401 North Michigan has been the high level of engagement and advanced technical training of building operations staff. Though decisions on these types of investments generally come from “top brass” at the management firm, it’s crucial that the people doing the work on the ground are brought on board and feel a sense of ownership on the project.
According to Anderson, the best way to get staff on board is to engage them early in the process and allow them to provide feedback based on their hands-on experience working with the systems and building components targeted for upgrades.
“I ask for ideas first and engage my crew,” Anderson says. “I start my meetings with, ‘Do you have anything you want to talk about?’ If they can bring something up before I do, then they have ownership over that and are more motivated to take on the project.”
Having a highly trained building staff is critical to building effective collaboration with management on any green investments. Anderson works closely with the training administrators at the International Union of Operating Engineers Local 399 as well as the Illinois Institute of Technology to facilitate outings for sustainability classes. Both institutions are fully accredited with the Illinois Community College Board and Higher Learning Commission, and courses cover a wide range of relevant topics. For example, trainees who complete Local 399’s Energy Conservation Class become certified City of Chicago benchmark verifiers.
“I lean heavily on my team’s expertise,” Anderson says. “The better they understand each building system and individual piece of equipment, the better prepared everyone is to employ sustainability measures.”
Large retrofit projects are great and afford many immediate savings, but Anderson has come to find out that “low hanging fruit sometimes grows back,” and that focusing on the team’s knowledge base and overall engagement ensures any and all operational savings opportunities are exploited as soon as they become available.
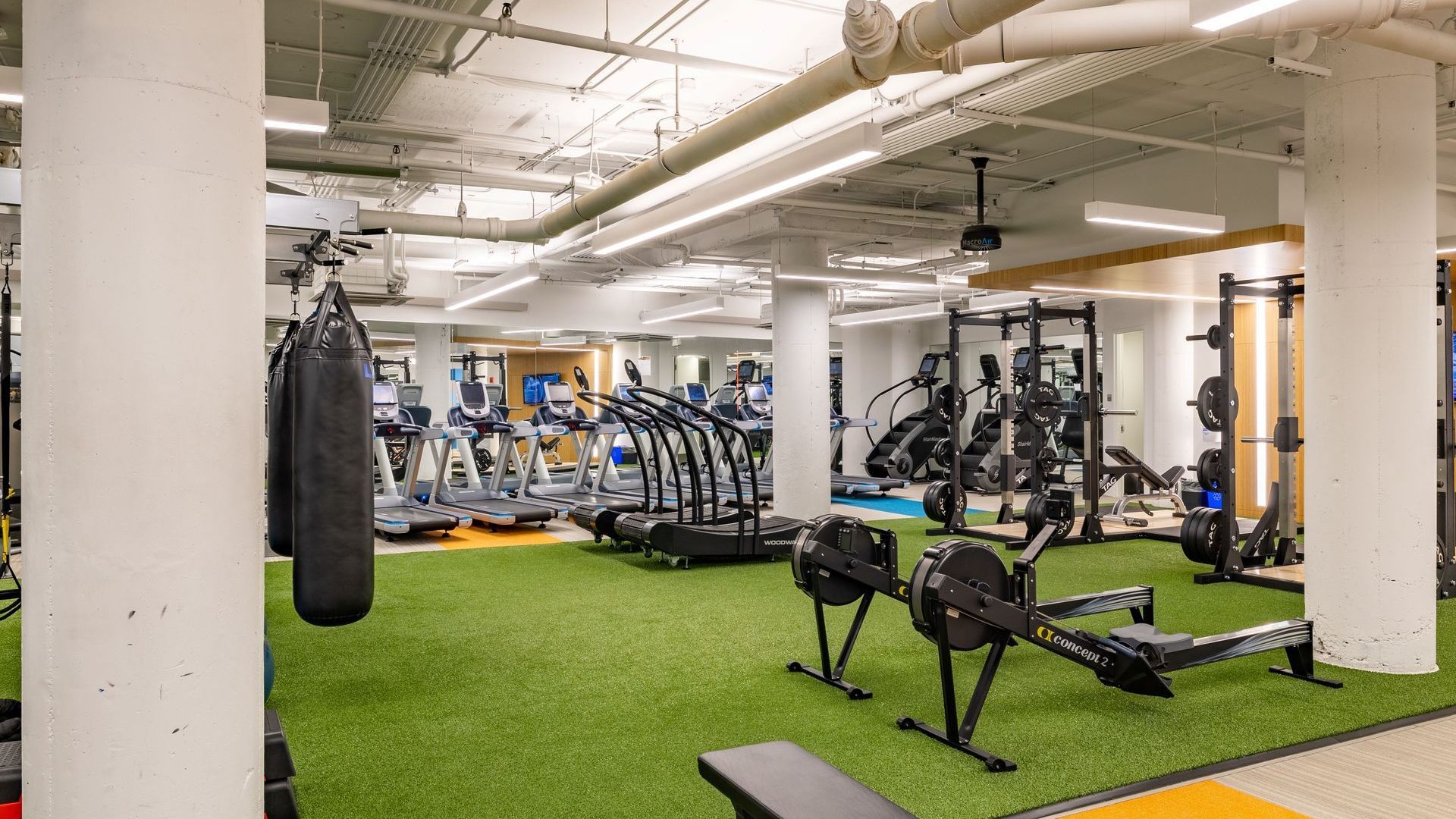
Results
During Zeller’s internal Energy Challenge—which encompassed many of the sustainability initiatives related to 401 North Michigan’s LEED Platinum recertification—the building was able to save $500,000 in energy costs over the course of three years. Many of the upgrades are tied to building automation and controllability of the building’s environment, which has allowed building staff to stay flexible and provide a clean, safe, and healthy working environment for occupants.
In total, the energy efficiency measures that were implemented as part of the 2022 LEED recertification process save the building 77,563 kWh of electricity annually.
Aside from the significant energy and cost savings, the sustainability upgrades that Zeller implemented also increased tenant satisfaction and comfort. The number of tenant complaints that management and operations at 401 North Michigan have received about issues with office temperature, for example, have dropped precipitously since the upgrades have been completed. Indoor air quality has also been improved
Green building certifications such as LEED also speak to the quality of the property asset as well as the commitment of building ownership and management. “LEED certification was considered critical to stay competitive for bringing in new tenants and retaining existing tenants,” Olson says. “Zeller has been successful on taking the lead on this initiative both at 401 North Michigan and throughout other buildings in our national portfolio.”

Lessons Learned
One of the biggest lessons that Zeller took away from investing in sustainability upgrades at 401 North Michigan has been the importance of staying on the cutting edge of these initiatives and demonstrating to decision-makers that the return on investment is worth the upfront costs.
“Don’t fall behind,” Olson says. “Even if there are no funds to support these sustainability projects, do your due diligence to understand the efficiency value, the potential economic impact as well as the economic return. That way, your team can present and defend the financial investment in a knowledgeable manner.”
For building operations staff like Anderson, the recertification process has only underscored the significance of continuing education. His team currently has four credentialed LEED Green Associates; two staff who are Building Operator Certified at Level 1 and Level 2; and two who are currently pursuing Certified Energy Manager designation. For his work maintaining 401 North Michigan’s status as one of the most sustainable buildings in Chicago, Anderson was also recognized as BOMA/Chicago’s 2021 Building Engineer of the Year.
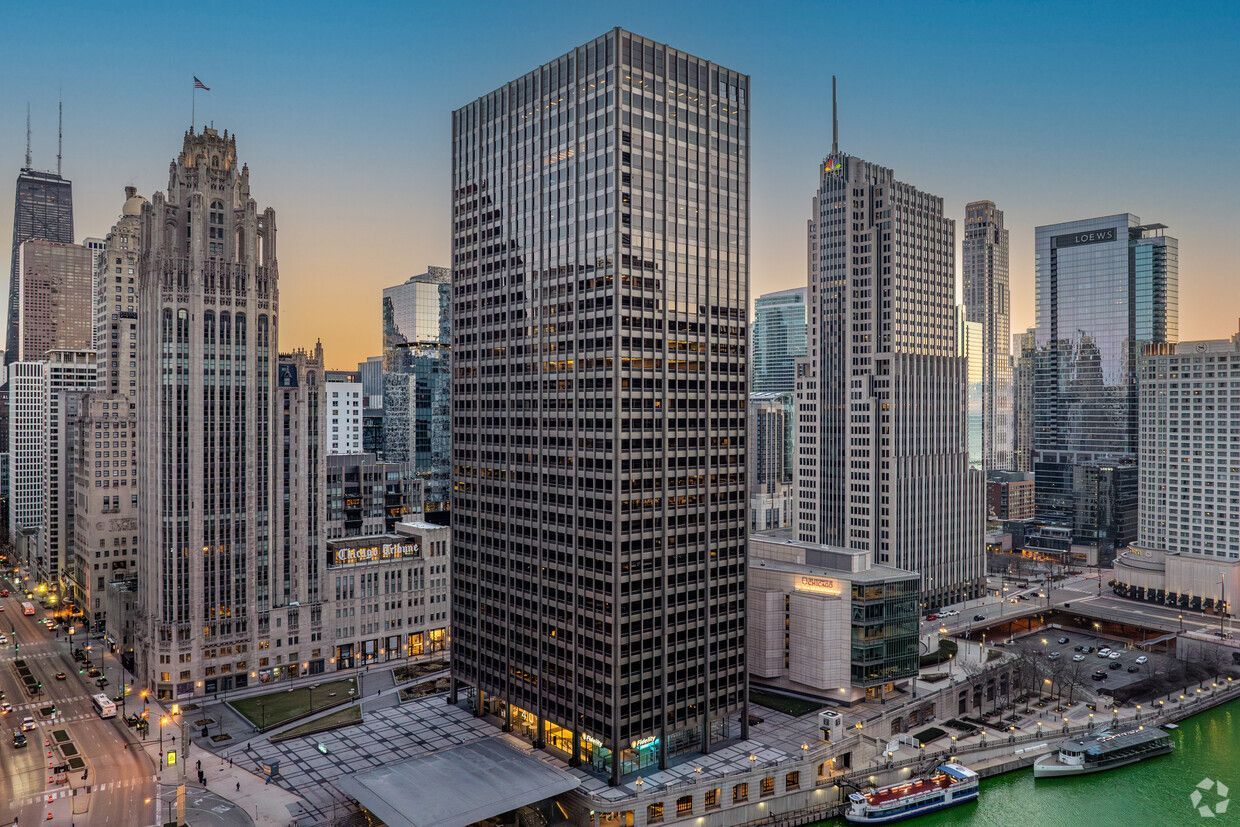